Objectives of Aviation Quality and Safety Management Systems
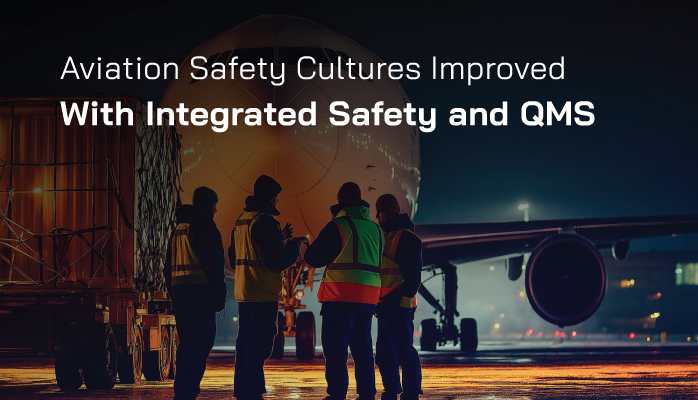
The objective of an aviation quality management system (QMS) is to continually improve the level of customer satisfaction by meeting their needs.
The objective of a safety management system (SMS) is to also continually improve, but instead of focusing on customer satisfaction, an SMS program focuses on stakeholders' safety, both real and perceived.
How can aviation safety professionals measure safety and customer satisfaction? Is that really a concern for the safety team? I doubt it.
Related Articles on Integrated Aviation SMS and QMS
- What Are Differences of Aviation Safety Management Systems (SMS) and QMS Programs
- 5 Easy Ways to Combine QMS and SMS in Aviation Operations
- 4 Things to Understand About QMS and SMS in Aviation Risk Management
Some objective measurements are easy, such as:
- Meantime to failure;
- Gross defect rate;
- Net defect rate;
- Productivity rate; and
- Turnover rate.
Unfortunately, safety and customer satisfaction are more nebulous and difficult to measure objectively. How do tell whether a company is safe?
- The low number of reported hazards or incidents?
- Low accident rate?
- Hazard identification and safety reporting rates?
Process Approach Heart of Safety & Quality Management Systems
Integrated safety and quality management systems strive to meet their objectives using the "process approach." Operators are in business to provide services. When aviation service providers have a monopoly, there is little incentive to improve processes, except for often inconsistent pressure from civil aviation authorities.
Aviation service providers operating in a competitive market achieve their objectives when their customers are happy and they feel reasonably safe.
Services they provide may include:
- Aviation maintenance repair and overhaul;
- Catering;
- Ramp services;
- Ground handling services;
- Ticketing and passenger-related services;
- Fueling; and
- Cargo.
Aviation service providers offer their services using either in-house or contracted labor, equipment, and buildings. A single activity or a group of interrelated activities is commonly referred to as a "process." Managing these processes to achieve the best outcome is what quality professionals refer to as the "process approach."
Related Articles on Integrated Aviation SMS and QMS
- QMS Programs vs Aviation Safety Management Systems (SMS)
- Moving From Quality Management to Integrated SMS and QMS Systems
- 5 Most Important Ways to Integrate Aviation SMS and QMS
SRM and SA Demonstrate Process Approach in Aviation SMS
Aviation safety management systems (SMS) also adopt the process approach. At the heart of each SMS are the safety risk management (SRM) and safety assurance (SA) processes. SRM is the design of the operators' "systems" which include:
- System description;
- Hazard identification documentation;
- Hazards risk consequences (expected potential harm should hazard manifest itself); and
- Risk controls.
Management needs assurance that each system design is achieving its goal as safely and efficiently as possible. This assurance comes from safety assurance activities. SA processes monitor the system design. Substandard safety performance is detected by:
- employees interacting with the system;
- managers routinely monitoring performance of the system; and
- auditors reviewing the system to ensure processes and procedures are being performed as designed.
These monitoring activities look for anything out of the ordinary. Discrepancies must be reported into the SMS as either
- reported safety issues or
- audit findings.
These reported safety issues and audit findings fall in the "Data Acquisition" box immediately under SA's system monitoring activities below.
As management reviews reported safety concerns, they will also review the affected systems to determine whether existing risk controls remain effective or require:
- replacement;
- enhancements;
- more scrutiny during regular monitoring activities; or
- support from additional controls.
When risk controls require modifications, the system will require formal documentation. This process is affectionately called "Management of Change" in aviation SMS. Instead of being a cowboy and implementing controls without careful consideration, there is a process to manage changes to the system's processes on the SRM side.
Related Aviation SMS Management of Change Articles
- Understanding Management of Change in Aviation SMS
- 7 Tips Safety Managers Use to Manage Change in Aviation SMS
- How to be Compliant With ICAO Change Management Requirement
Process Approach May Be Overlooked in Aviation SMS
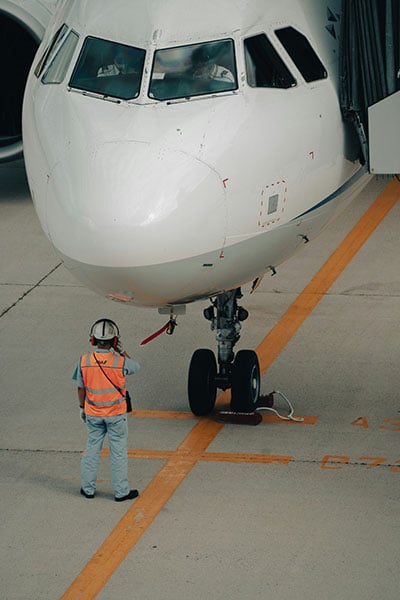
The process approach is often overlooked by aviation safety professionals because it is seldom taught in conventional aviation SMS training courses. Safety professionals will have more control over the entire chain of interrelated processes when using the "process approach."
Safety professionals adopting the process approach understand the importance of:
- Understanding and continually meeting stakeholder requirements;
- Concepts of added value when evaluating processes and systems;
- Measuring performance and process effectiveness; and
- Continual improvement based on some type of measurement.
The last point may be difficult to prove in a safety management system, especially when safety managers do not have access to professionally designed aviation SMS database tools. Unless you can measure it, how does one know where he is today? Safety managers are not always "safety professionals" when they begin their term as the "director of safety" or "safety manager."
Newly minted safety officers are initially struggling to understand:
- SMS requirements;
- how (and whether) organizational goals and objectives align with the SMS implementation;
- how the organization currently complies with those SMS requirements;
- what obstacles impede smooth SMS implementation; and
- what resources are available to further implement or promote the SMS.
Unless these safety managers have previously seen an SMS, there is little chance that the SMS' data management strategies will be properly addressed during the initial SMS implementation steps. I would venture to guess that every aviation safety manager misjudges the level of SMS documentation required to support the SMS to demonstrate continuous improvement of the SMS. Consequently, initial SMS implementations lack the ability to effectively monitor SMS performance.
Quality management systems strive for objective measurements, but objectively measuring the effectiveness of particular elements of the SMS and the effectiveness of corrective actions can be difficult or nearly impossible in the short term. Therefore, continuous improvement of certain processes must be measured subjectively and repeatedly.
For example, safety managers can easily measure their safety reporting culture. This is commonly achieved by counting the number of safety reports within a given time period and dividing the number by the number of participants (or employees).
Evaluating safety reporting cultures is very straightforward and objective. However, judging a safety culture is more difficult and observers rely heavily on soft skills requiring introspection, perception, and feedback from fickle subjects. Safety culture surveys are used to obtain more objective results.
Related Aviation Safety Culture Articles
- What Is Safety Culture in the Aviation Industry?
- How to Build Safety Culture in Aviation SMS
- How to Tell Your Safety Culture Needs Help? - With Aviation SMS Resources
Positive Safety Cultures in Aviation SMS
Unlike auditing a particular department or division for a specialized subject area, safety cultures affect entire organizations, from the
- accountable executive to
- mid-level managers to
- line-level employees to
- contractors and vendors supporting your operations.
Aviation service providers with the highest safety ratings display a constant concern about safety. This constant concern for safety is tightly interwoven into their organizational culture. SMS implementations fail whenever management treats aviation SMS like a traditional safety program. You may remember these traditional safety programs. These safety programs had:
- no (or very little) expectation of returning value on the investment;
- no commitment requirement from management;
- no regular and formal performance monitoring requirements;
- no protection from management;
- no expectation of measuring or demonstrating continuous improvement; and
- little sincere, sustained effort to change safety cultures.
An SMS is different from traditional safety programs. SMS has well-defined risk management processes that work effectively with organizational quality issues. After all, SMS is modeled after quality management systems, so there should be little surprise that many of the processes are similar, except with a focus on safety rather than quality.
If you are already focusing on quality management in your company with a formal QMS, there is a strong chance that you have tools that can be used to support the SMS, such as data collection and measuring software. There is also a high probability that safety culture has been ignored in favor of production goals.
To test the heartbeat of your safety culture, routine safety culture surveys have proven effective. The key takeaway here is "routine," meaning that safety managers must follow up year after year in order to measure results that may be skewed in the early stages of safety culture surveys.
Related Articles on Safety Surveys in Aviation SMS
- Aviation SMS Surveys - an Often Neglected Safety Promotion Tool
- How Safety Officers Benefit From Aviation Safety Surveys - Free Templates
- 5 Characteristics of Effective Aviation Safety Cultures - With Free Survey
Safety & Quality Managers Seldom Follow Through on Culture Surveys
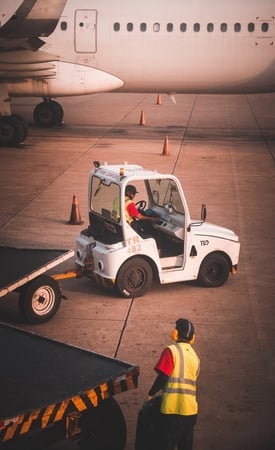
As noted above, routine safety and quality culture surveys should be performed on a regular basis. Annual cultural surveys seem to be the norm for aviation service providers engaging in these surveys. It would be interesting to learn the true motive behind safety culture surveys. Are they performed due to oversight pressure? Or do you think safety managers are really interested in promoting the aviation SMS?
I think there is a bit of both going on. Safety culture requires considerable time to change. Improving safety culture is not considered "low-hanging fruit" in an SMS. The low-hanging fruit in an SMS implementation is:
- Safety policy (which strongly affects safety culture);
- Safety reporting system (which also affects safety culture);
- Non-punitive reporting policy (definitely shapes safety reporting culture);
- Defining safety accountabilities and responsibilities;
- Performing the gap analysis; and
- Drafting an SMS implementation plan.
Before you go off and conduct a safety culture survey, review the above "low-hanging fruit" to determine how they currently affect safety culture. Do not make any sudden changes before you conduct your surveys. You want a "stable system" to evaluate. Sudden changes to the safety reporting system or the non-punitive reporting policy before conducting a survey don't allow for a good "baseline measurement."
Based on empirical evidence, operators seldom have more than three years worth of survey data.
The reason is that:
- Processes for conducting cultural surveys are ill-defined;
- Processes lack oversight;
- Data management processes not developed for long-term monitoring strategies; and
- Safety and quality managers seldom stay in the same position for more than three years.
An SMS is not a fad. In order to realize the same benefits from the SMS as operators do from their QMS, they need to consider SMS implementation as a significant financial driver. Investments in data collection and data mining strategies are important to spot trends and to prevent "The Accident."
The FAA eloquently sums up the objective for SMS in their 14 CFR Part 5 regulations. They state that the:
objective of Safety Management Systems (SMS) is to
- proactively manage safety,
- identify potential hazards,
- determine risk, and
- implement measures that mitigate the risk.
The FAA envisions operators being able to use all of the components of SMS to enhance a carrier’s ability to identify safety issues and spot trends before they result in a near-miss, incident, or accident. For this reason, the FAA is requiring carriers to develop and implement an SMS. (emphasis and formatting added)
Source: Federal Register / Vol. 80, No. 5 / Thursday, January 8, 2015 / Rules and Regulations
Operators that have existing QMS data collection tools have a distinct advantage over smaller and medium-sized operators that have not implemented quality management systems. Operators with a QMS have existing database tools to identify safety issues and spot trends. This does not mean that you should go out and implement a QMS before you start on the SMS. The accountable executive may become frustrated with your game plan.
However, if you don't have a QMS, but you want to benefit from the same process-driven methodologies that come with QMS, then there is a shortcut to having both.
While implementing the SMS, focus on tools that support both the SMS and QMS. There are low-cost, commercially available SMS databases that support both SMS and QMS processes.
Commercial SMS databases are designed to manage all SMS processes, including SRM and SA. Yet an SMS database is very powerful and functionality can be extended to other areas of your operations. These same SRM and SA processes that you are required to implement to demonstrate a performing SMS can also be used to address additional business concerns, such as
- Security;
- Environmental;
- Compliance;
- Customer service; and
- Quality of operations.
The tragedy I see is that MOST operators are too short-sighted to see an opportunity in disguise. While they are implementing SMS, they should be focusing on the big picture:
- how do we capitalize on this SMS requirement?
- how do we take this extra SMS implementation burden and turn it to our advantage?
This is a healthy, proactive mindset.
I am finally seeing a younger generation of managers realize this fact. And I'm delighted.
I'm hoping the industry wakes up and earnestly embraces these SMS concepts. So the short take is: don't neglect SMS data management strategies.
An SMS database should be implemented sooner rather than later, as there are many advantages an SMS database can provide as you seek to improve the quality of your operations without an existing QMS. You can turn your SMS into a financial driver. But you need to focus on the processes and make them as efficient as possible. Otherwise, you will be simply wasting fuel taxiing.
Related Aviation SMS Database Articles
- 5 Most Important Things to Know Before Buying Aviation SMS Database
- Tips Writing SMS Manuals With Aviation Safety Database Solutions
- Pros and Cons of In-House SMS Database and Off-the-Shelf-Solutions (COTS)
Final Thoughts on Adopting Processes for Quality & Safety Cultures
Quality management programs are great at defining processes and managing these processes. From what I have seen in many safety management programs, there is often a lack of defined processes to ensure the continuity of certain programs, especially when safety managers leave the company.
By using integrated aviation safety and quality management database software, there will be less chance that programs fail when safety managers leave the company. Integrated QMS and SMS software programs also provide tools that assist managers in conducting cultural surveys on a scheduled basis.
When a process is too difficult to repeat, employees will seldom be able to continue the process as the years pass. This is especially true when processes are repeated annually.
Considerable time passes between cultural surveys. Therefore it is easy for managers to overlook the importance or forget to carry out the surveying task without adequate controls in place.
Hopefully, the controls will be automated tools coupled with upper management oversight.
SMS database tools increase the effectiveness of safety managers. If you want to demonstrate a professional SMS implementation, your chances increase when you have professionally designed SMS software tools. You immediately gain access to industry-accepted workflows developed and tested by hundreds of safety professionals.
Since 2007, SMS Pro has been working with aviation service providers around the world. We can help you achieve your SMS goals.
Please watch these short demo videos to learn how you can benefit immediately from better SMS database tools.
Live SMS Pro Demo
Have questions? Want to see SMS Pro live? Sign up for a live demo.
Last updated July 2025.