Identifying Mistakes Aviation SMS Implementations
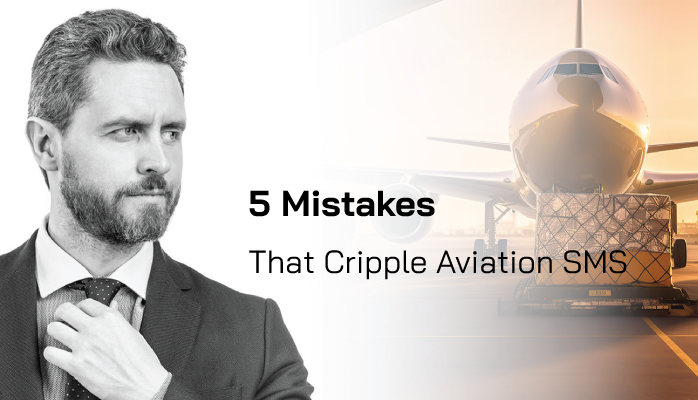
Successful aviation safety programs are self-conscious. That is, safety management teams are extremely sensitive to potential pitfalls and work hard to avoid needless mistakes.
Of course, in the real-world practice of safety management, “needless mistakes” are seldom easy to identify ahead of time.
Avoiding needless mistakes in aviation safety management systems (SMS) requires that:
- Decisions to be backed up by experience and data;
- Safety management teams seek out mentors and guidance from within the industry; and
- Safety managers use the myriad of industry-wide resources at their disposal.
While this sounds fairly straightforward to do on paper, actually taking the time to pursue these points requires time and energy that, frankly, safety managers may not feel they have the time or energy to always do.
Related Aviation Safety Manager Articles
- What Makes a Good Aviation Safety Manager?
- Hardest Challenges of Safety Managers in Modern Aviation SMS
- 5 Types of Aviation Safety Managers
But here’s the thing, shortcuts make long delays. In the end, making mistakes that could have been otherwise avoided will end up costing more time and money than if safety management teams had done their careful due diligence before making the decisions that led to the mistake. Here are 5 common mistakes that we see regularly and can significantly set back your SMS implementation's ability to perform and/or improve.
1 – Little to No Safety Performance Accountability
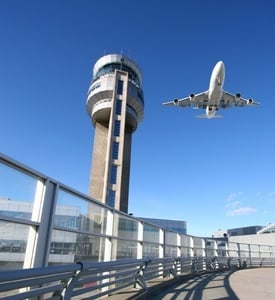
I’ll keep this one short because it speaks for itself. However, we must discern how we use the term "accountability."
Accountability in this section refers to employee involvement in SMS activities.
Operators define accountability in this sense by ensuring all line-level employees are aware of their role in the SMS and require active participation in the SMS. Furthermore, operators must promote these accountabilities to all employees. Remember, if the activity is not documented, it did not occur. This includes safety promotion activities. SMS accountabilities can be broadcast using:
- Newsletters; or
- Safety messages.
While promoting the accountabilities is great, how do you document that the employee understands their accountabilities? Again, if it isn't documented, it didn't happen. I find the most convenient opportunity to fulfill this requirement is during initial and recurrent SMS training.
When you are providing SMS training to reinforce accountability, make sure you cover their SMS responsibilities and accountabilities. But make it personal. Basically – what’s in it for the employee? If employees don’t have strong personal reasons and incentives for being active and involved in the aviation SMS, then they simply won’t be accountable for their safety performance. Safety accountabilities influence safety culture.
It’s critical for SMS success that employees know that:
- Safety performance is integrated with their overall performance (i.e., it could be the difference between receiving a raise/promotion, or could potentially cost them their job);
- Safety performance is being monitored; and
- They have common safety goals to work towards.
Simply put, safety needs to be a regular, core part of any aviation professional's job duties. Programs that rely on the idea of “safety for the greater good,” without any personal incentives for doing so, will be hard-pressed to facilitate change.
Monitoring employee safety performance is not a one-size-fits-all approach. Choosing which metrics to monitor requires only a bit of common sense. Metrics chosen for employee SMS performance monitoring should be under the direct control of each employee. For example, using an "accident rate" or "bird strike rate per 100 flights" to evaluate the performance of the safety manager should not be considered. Safety managers have no direct control over employee behavior or bird strike rates.
Taking the case of the safety manager, we should look for performance monitoring metrics that the safety manager does have direct control over, such as:
- Number of investigations completed on time;
- Increase in number of safety reports entering safety reporting system; or
- Number of safety promotion campaigns initiated within a particular time period.
The above performance monitoring metrics will not be a good choice for operational department heads. For department heads, you may select:
- Number of safety reports coming from their department compared to last year;
- Percentage of reported safety issues completed on time per company policy; or
- Percentage of hazard analysis activities completed on time.
For line-level, non-managerial employees, the following metrics will serve as an example:
- Were safety policies reviewed within the past year?
- Percentage of assigned safety tasks completed on-time;
- Number of safety reports submitted compared to organization's average number of reported safety issues per employee;
- Percentage of safety meetings employee attended that were required; and
- Has the employee reviewed and accepted their safety accountabilities within the past year?
Related Aviation Safety Performance Articles
- 5 Useful Safety Performance Monitoring Tools in Aviation SMS
- 4 Pillars | How to Conduct Safety Performance Monitoring and Measurement
- 7 Charts to Monitor Employee Safety Performance in SMS
2 – Recreating the Wheel
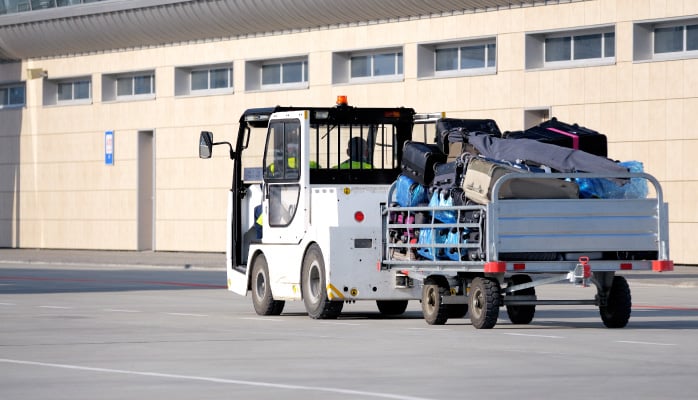
Here’s an all too common scenario. A safety professional is put in charge of starting an SMS implementation in their operation and being the responsible safety manager. They spend a lot of time
- researching requirements,
- creating standard policies and procedures,
- mapping an org chart,
- planning communication channels and
- safety reporting options, etc.
Long story short they build the basic structure of an SMS in the form of an SMS handbook. The handbook gets approved and a safety budget is established. At this point, their SMS risk management processes are completely manual, which is far from ideal, so the safety manager goes shopping for tools, such as aviation SMS software.
Then suddenly a cold reality sets in the processes of acquired SMS tools that are very different from the ones that the safety manager created. The workflows and communication methods are different from the safety manager's documented risk management workflows. The entire safety manual is going to have to be revised.
All that time, energy, and consideration for creating the SMS structure – wasted. That’s a headache, it will stall SMS implementation progress, and it will eat up the budget. If budgets are small, trying to adopt tools can simply become impossible at this point.
We run into this scenario constantly. When safety managers are implementing SMS, they should always:
- Select their aviation SMS data management tools in the first phase of the SMS. A totally integrated SMS database is best, but if that is not realistic for a budget then the essential risk management tools should be chosen (i.e. safety reporting system, risk management system, etc.); and
- Build the SMS around the core tools.
This will save a considerable amount of time and budget, and it will ensure the risk management processes of your core performances – such as safety reporting and risk management – will be industry-honed and tested.
For safety professionals who want to implement their SMS properly the first time around, low-cost, commercially available SMS software is the fastest route to full SMS implementation. The most popular commercial SMS software has been accepted by civil aviation authorities for many years. There is no sense in recreating the SMS wheel when an operator can acquire an SMS database that has proven, industry-accepted risk management processes.
Related Aviation SMS Software Articles
- How to Choose Aviation SMS Software - Educating SMS Professionals
- How Does Aviation Safety Software Improve Safety? - Aviation SMS
- 20 Benefits of Aviation SMS Software
3 – Neglecting the Evaluation of Aviation Safety Culture
Aviation safety culture seems to be one of those things that are discussed and considered very important in safety management but have very little follow-through in actual practice. For example: what are you doing and/or what metrics are you using to evaluate safety culture in your SMS implementation?
If you are evaluating your safety culture, how do you know your evaluations/metrics are effective and accurate? I’m guessing very few readers have strong answers for either question.
The reason that safety culture evaluations are often neglected is because of safety culture:
- Seems more of a concept than tangible behaviors; and
- Seems difficult to objectively measure.
The fact that the highest safety-rated airlines and airports are constantly vigilant about safety indicates that they consider safety culture a high priority. Important decisions should be made in direct response to how safety is being practiced in your organization. Making decisions without working knowledge of safety behavior and safety attitude in your SMS is likely to lead to:
- Ineffective policies and procedures;
- Delayed or plateaued SMS implementation; and
- Stalled safety improvement because behaviors have stagnated.
Safety culture should be dynamic. One great real-world use of evaluating safety culture is:
- Sending out safety surveys on a consistent basis (i.e. semi-annually, etc.) with the same questions (yes/no or multiple choice questions) – ideally the survey would be short;
- Collecting the data;
- Map the data over time, such as on a line graph.
We have seen this method used with great success. Moreover, this data can be seen visually.
Related Articles on Aviation Safety Culture
- What Is Safety Culture in the Aviation Industry?
- How to Build Safety Culture in Aviation SMS
- 3 Reasons Why Aviation Safety Culture Leads Directly to Safety Performance
4 – Lack of Defined Processes (Creates Dependencies)
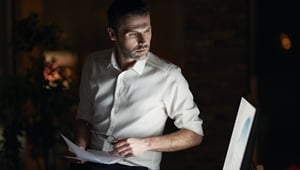
Years ago I worked with a startup company whose primary goal at the time was to solidify the internal processes that kept operations running smoothly. This happened through the creation, revision, and documentation of all the company's various processes. The whole point of creating so much system process documentation was to ensure that the success of operations was dependent on systems rather than people.
The goal of any documented process is that someone completely unfamiliar with the system could follow the documentation and complete a task successfully. Aviation SMS processes should be treated with the exact same level of attention. In aviation SMS, approaching safety operations in this manner is known as the “process approach.”
Unfortunately, the process approach is, in many organizations, undervalued. Such organizations have processes that are either vague, don’t match real-world practices, or are non-existent. Lack of defined processes will usually:
- Create an aviation SMS that is more dependent on the abilities of individual people (and what happens when they are gone?);
- Seriously limit the growth potential of an SMS;
- Open the organization to needless risks, such as in the event of employee turnover or when SMS managers leave; and
- Hurt the ability to perform well on aviation safety audits.
Well-documented safety processes will ensure that:
- New employees can quickly get up to speed and follow best safety practices right away;
- When a safety manager leaves the company, safety operations can continue as normal; and
- That risk management processes are reproducible, more manageable, and standardized.
Related Articles on Aviation Risk Management Processes
- 3 Main Components of Aviation Risk Management
- 8 Stages of Safety Events in Aviation Risk Management Programs
- What Is the Process of Risk Management in Aviation SMS
5 – No QMS and SMS Integration
I realize that this is a bit of a controversial subject, but we have maintained in the past that integrated quality management systems (QMS) and safety management systems (SMS) have strong potential to improve safety management in aviation.
One of the reasons is the above-mentioned process approach. QMS are usually much better at standardizing processes for maximizing customer satisfaction in airports and with airlines. Integrating the QMS process approach in aviation safety programs has strong potential to improve safety performance, as discussed above.
Moreover, integrating QMS and SMS mitigates the likelihood of the following dangers:
- Disparity in focus between QMS and SMS (i.e. production performance is stressed over safety practices) will hurt safety culture by sending the message that production performance trumps preparedness;
- Potentially costly repercussions from following QMS processes that interfere with best safety practices; and
- Sending mixed/conflicting messages to front-line employees about their top priorities while completing tasks.
Lack of QMS and SMS integration has the potential to stall or greatly stunt the continuous improvement of aviation SMS. Smaller companies with fewer than 300 employees seldom consider an integrated SMS and QMS. Larger companies may already have QMS implemented. In these cases, many of the data management tools can be extended to support the SMS implementation.
Final Thoughts on Mistakes in SMS Implementations
Without a doubt, I'm certain that I have hit on at least one of your pain points. There are certainly more pitfalls for SMS implementations, but these are certainly worth your consideration.
Don't become too concerned if your SMS is a failure at this point. There is hope. More than once I have seen failed SMS implementations that have had to restart the process. While it is not ideal, restarting an SMS may be seen as the "smart move" for stagnating SMS implementations. If you are entertaining this idea, first take your concerns to the accountable executive. Be prepared. Layout the facts. Listen to the accountable executive's goals and objectives to ensure that they align with the SMS' goals.
One of the biggest frustrations for safety managers is not having the proper tools to manage the SMS documentation requirements. This is like sending an aircraft mechanic to service an aircraft without the proper tools. It is unthinkable and is certainly too risky. The same concept applies to SMS implementations. Safety managers need the proper tools if the accountable executive aspires to have a fully functioning SMS implementation...with benefits.
The alternative? At best, a paper SMS.
Good luck.
To see an example of the best integrated Safety-Quality Management Solution, check out these short demo videos.
The Safety-Quality Assurance Solution is built on a foundation of a best-in-class aviation SMS database. This is not a beginner's toy or an auditing solution with a few risk management tools added. This is a full-featured Safety-Quality Management Solution. If you want the second best, don't look at these tools.
Last updated in December 2024.