Purpose of Root Cause Analysis
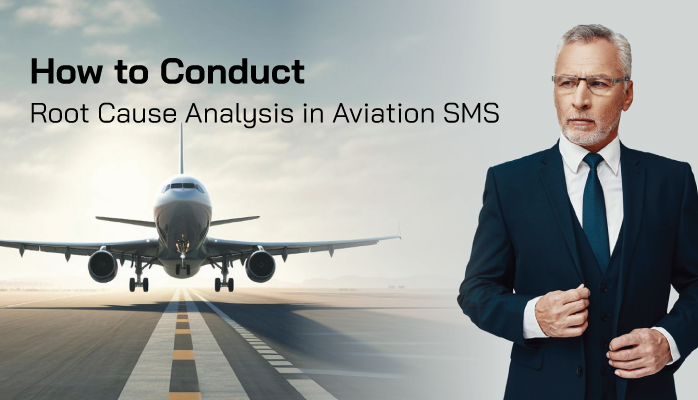
Aviation safety managers usually have different opinions about exactly what root cause analysis is.
Root cause analysis activities for one safety manager may not align with the risk management processes practiced by another. This is because, in aviation safety management systems (SMS), there is no standard definition for what root cause analysis is.
Even oversight agencies like the FAA or ICAO shy away from providing much guidance on what root cause analysis is or how to conduct it.
Related Articles on Root Cause Analysis in Aviation SMS
- Proactive Risk Management: What Root Causes Say About Management
- Is Root Cause Analysis Proactive or Reactive?
- 3 Methods for Root Cause Analysis in SMS Programs
The reason that regulatory agencies don't offer guidance on how to perform a root cause analysis goes back to the philosophy of:
- Provide the operators with the requirements, but
- Don't tell them how they must address the requirements to meet compliance.
As we all know, aviation service providers vary widely in:
- size (number of employees, aircraft, operating locations);
- industry segment (airline, airport, flight school, aviation maintenance organization, FBO, manufacturer);
- operating budgets;
- safety culture; and
- risk management philosophies.
Attempting to provide compliance guidance is filled with too many variables and possibilities to consider.
Definition of Root Cause Analysis?
The lack of definitive guidance from regulatory agencies is not necessarily a bad thing. To arrive at "what is a root cause analysis" may be easier if we discuss the intent of the activity. What’s most important for us to understand are the goals and purpose of root cause analysis:
- Understand why the safety event happened;
- Establish precursors to danger; and
- Establish underlying causes for safety issues.
With varying levels of success, different aviation SMS will accomplish these goals. Organizations may use:
- Bowtie analysis;
- Cause and effects analysis;
- Contributing factors' analysis;
- 5 WHYs analysis; or
- Fishbone diagrams.
Understanding the specific goals of root cause analysis will allow safety managers to be more effective in establishing root causes in their reactive risk management activities.
Related Reactive Risk Management Articles
- What Is Reactive Risk Management (Why It’s Essential for Aviation SMS)
- Going From Reactive to Predictive Risk Management in Aviation SMS
- From Reactive to Proactive Risk Management in Aviation SMS
How to Know When You Have Arrived at Root Cause
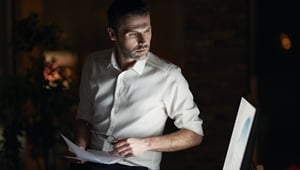
Perhaps the biggest mistake or misunderstanding people make when performing root cause analysis is understanding where to stop when looking for root causes. Managers will either:
- Not go far enough: the identified root causes actually have further underlying causes; and
- Go too far: the identified root causes are generalizations of precursors to danger.
With root causes, you are basically repeating the following basic steps:
- Analyze a circumstance; and
- Ask, “Why did this happen?”
This process will be repeated over and over until the root cause is identified. You know when a root cause has been identified when your answer to “why” is:
- Simply because it is.
What this means is that root causes will have no specific reason for being present that is within anyone’s control. Or, there will be no discernible explanation for “why.”
Here are three ways to conduct root cause analysis in aviation SMS.
5 WHYs Analysis
5 WHYs analysis is one of the most common ways to perform root cause analysis. 5 WHYs essentially involve starting at the hazardous condition, and asking, “Why did this happen.” Each time you ask, you will write down the answer. For each answer, you will repeat the question. This question is generally repeated 5 times until you arrive at the root cause(s).
There are several pros to this method of establishing root causes:
- Simple to understand;
- Quick to perform; and
- Provides a direct lineage of circumstances.
The cons of this method are:
- No visual cues for easy reference;
- Impossible to trend when solely relying on narratives;
- Cumbersome to associate and track as key performance indicators (KPIs); and
- Tends to be a “narrow look” at safety events.
The 5 WHYs analysis is a good way to start performing root cause analysis before adopting a more robust analysis technique during the risk management process.
Related Aviation Risk Management Articles
- 3 Main Components of Aviation Risk Management
- 5 Signs of Good Aviation Risk Management Training
- How to Prepare Data for Trend Analysis in Risk Management Programs
Fishbone Diagram
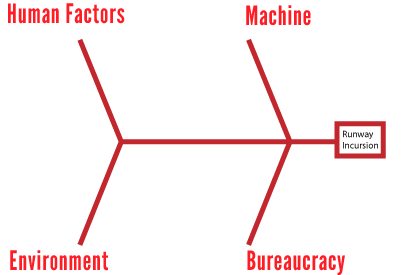
Fishbone diagrams, also known as cause and effect diagrams, are another popular root cause analysis technique.
A fishbone diagram derives its name from its fishlike appearance, with a head and several fins. Each “fin” or “branch” of a fishbone diagram describes a different category of the situation. The most common categories used in aviation SMS databases are:
- Human;
- Machine;
- Systems;
- Policies and Procedures;
- Materials;
- Organization; and
- Environment.
The head of the fishbone describes the hazard/Top Event.
The pros of fishbone diagrams are:
- Very comprehensive, and identify all major/minor root causes;
- Visual diagrams are useful for future reference;
- Easy to understand by upper management; and
- Break down root causes by type.
The cons of fishbone diagrams are:
- Not much explanation or justification for each level of analysis;
- Not suitable for every reported safety issue that comes into the risk management workflow;
- Increase complexity of risk management processes for smaller operators; and
- Easy to get sidetracked and identify root causes that are not necessarily directly relevant to the current issue.
Fishbone Diagrams should be used for safety managers who want the “whole picture” of safety events. It should be used by safety managers with experience performing root cause analysis and are able to discern valid and not-valid root causes.
Related Articles on Using Fishbone Diagrams in Aviation SMS
- Pros and Cons of Fishbone Diagrams in Aviation SMS
- How to Create Fishbone Diagrams in Aviation SMS in 5 Steps
Bowtie Analysis
Bowtie analysis is a very in-depth technique for performing a root cause analysis. The bowtie analysis involves establishing a Top Event, which is similar or the same as Risk Events or Hazards. Next, you will work backward to identify the major event markers and risk controls.
The pros of the bowtie method for root causes analysis are:
- Fantastic for identifying all major root causes;
- Understand how root causes work against SMS programs to produce mishaps; and
- Great visual reference for understanding the “bigger picture.”
The cons of bowtie analysis are:
- Can be hard to understand; and
- Error prone and time-consuming.
Bowtie analyses are best reserved for high-risk issues and experienced safety managers. On low/medium risk issues, bowtie analysis is probably overkill and the before-mentioned techniques are usually more efficient.
Related Bowtie Analysis in Aviation SMS Articles
- How to Do Bowtie Analysis in Aviation SMS – 5 Step Walkthrough
- 6 Essential Rules for Bowtie Analysis in Aviation SMS
- 3 Ways You’re Not Using the Bowtie in Aviation SMS
Final Thought: Choosing Root Cause Analysis Technique
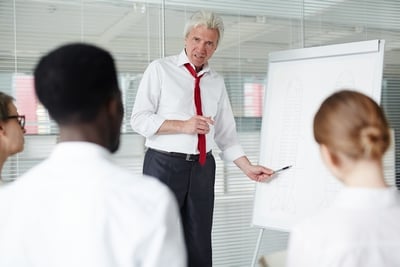
Chances are you already using at least one of these root cause analysis techniques. The generic 5 WHYs technique for root cause analysis seems to be the most popular for aviation service providers around the world, regardless of industry segment.
SMS database software may come loaded with these risk management tools. For example, every SMS Pro product comes with:
- 5 WHYs template;
- Fishbone diagrams;
- Causal factor analysis.
Most SMS Pro clients prefer the 5-Whys over other techniques because the analysis is fast and easy to explain to management that has previous quality management training.
Many companies choose to adopt a more specific approach to meet their needs when:
- Their safety management team becomes adept at performing the 5-Whys; and
- They want a different type of root cause documentation that other techniques provide.
If your company meets these criteria, consider adopting a new technique to see how it fits with company goals.
Special software is not required to conduct a root cause analysis; however, an SMS database does come in handy as a time and labor-saving tool. Documenting investigations and generating reports based on historical trends is made much simpler and provides more consistent results when using an SMS database.
If you are looking for SMS software, this is commonly one of the first things clients ask for when shopping for an SMS database. Make sure the workflows are complete and flexible for conducting a root cause analysis in your investigations.
Do you have an SMS database? Does it allow you to easily determine the root cause and document your findings?
To see one of the more popular SMS databases with all the tools mentioned here, please watch the following demos. If it looks like we are a good fit for you, we'd like to become your SMS Partner.
Live SMS Pro Demo
Do you like what you see? Since 2007, we have been providing the best aviation SMS database software on the market. Each day, I become more confident that SMS Pro is the best database software because our clients have been repeating this same story for years. I'm beginning to believe them.
For another new analysis method that is extremely helpful in clarifying failures in SMS programs in safety issues, see this free e-book covering Shortfall Analysis:
Last updated in September 2024.