How to Conduct Root Cause Analysis
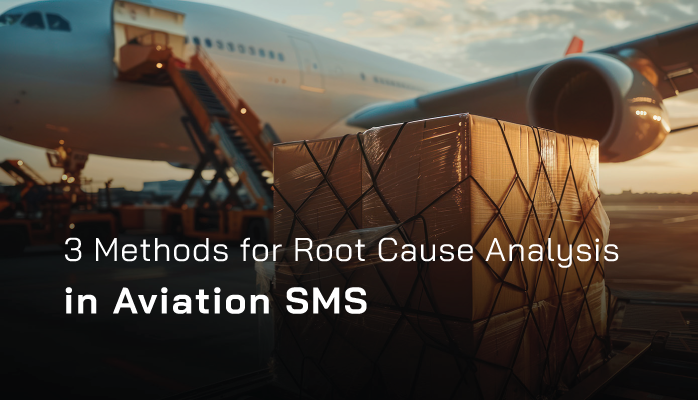
Every aviation safety management system (SMS) contains a subsystem to manage risk associated with reported safety issues and audit findings. This subsystem can be called the SMS' risk management system as this system provides the logical workflow necessary to efficiently:
- Conduct and document investigations;
- Assign and track corrective actions and preventive actions;
- Perform risk assessments; and
- Classify the event for future trend analysis reports.
Related Articles on Trend Analysis in Aviation SMS
- Six Steps How to Perform Trend Analysis in Aviation SMS
- How to Prepare Data for Trend Analysis in Aviation SMS
- How to Use Trending Charts in Aviation SMS
Root Cause Analysis in Risk Management Life Cycle
Reported safety issues and audit findings enter the SMS risk management system. The risk management system provides a repeatable process to run safety issues through the organization's documented risk management processes. These processes may be manual or facilitated by the use of SMS database software.
Aviation SMS databases provide operators with repeatable workflows and tools to track and document the safety teams' risk management activities. Most aviation service providers benefit from SMS databases in that accountable executives, operational department heads and safety managers can more easily monitor organizational safety performance with the use of real-time dashboards or predefined charts and graphs.
Most commercially available SMS databases also have sophisticated modules to conduct in-depth investigations that include documentation capabilities for:
- Investigation team;
- Investigation-specific images;
- Sequence of events;
- Causal factor analysis;
- Human factor analysis; and
- Root cause analysis.
Each safety issue that is processed in the risk management system has a life cycle. Some safety concerns may require an in-depth investigation, while minor issues may not warrant a full-blown investigation. During the investigatory process, a root cause analysis may be performed by:
- Safety managers;
- Safety analysts;
- Safety committee; or
- Assigned responsible manager (usually the department head).
What Is a Root Cause Analysis? The Standard Definition Is...
Root cause analysis for one aviation safety manager is not root cause analysis for another safety manager. What I'm trying to say is that there is no standard definition or process for root cause analysis in SMS guidance materials.
This lack of standardization is not a negative thing, as it gives aviation service providers the flexibility to create a process that best fits them. In anticipation of this, oversight agencies like the FAA or ICAO provide little guidance on how to conduct a root cause analysis.
It’s less important to “define” root cause analysis than to understand how you can use a method to meet root cause analysis goals. Root cause analysis is performed by adopting a method, such as:
- 5-Whys analysis;
- Bowtie analysis; or
- Fishbone diagrams.
Either of these methods will be used to:
- Understand the base mechanisms contributing to a safety event;
- Establish precursors to dangerous conditions (i.e., hazards, risk events, etc.); and
- Discover underlying causes contributing to safety/exposure in the operator's "system."
Below, we will take a more in-depth look at three methods for root cause analysis while running safety issues through your risk management life-cycle.
Related Root Cause Analysis Articles
- How to Conduct Root Cause Analysis in Aviation SMS
- Proactive Risk Management: What Root Causes Say About Management
- Understanding "Root Cause Analysis" Charts in Aviation SMS Dashboards
1 – How to Create Fishbone Diagrams
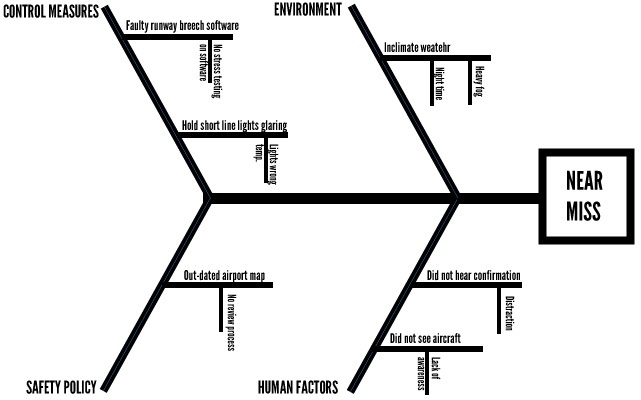
Fishbone diagrams, also known as cause and effect diagrams, derive their name from the fish-like appearance of a completed diagram. Fishbone diagrams are also known as cause and effect diagrams and Ishikawa diagrams.
These diagrams have:
- A “head,” which is your hazard/risk event;
- 4-6 “fins” which are the categories that you are using to organize root causes of a safety event (e.g., Man, Machine, Mission, Management, etc.);
- Fins can be a predefined model, such as 5-M or SHELL, or a custom model created by you;
- Each fin will have multiple “branches”; and
- Each branch may or may not have sub-branches.
Filling out these diagrams simply involves looking at the safety issue from the perspective of each fin (category), and establishing the relevant factors (branches). Next, for each branch, establish the reasons (sub-branches) that the branch exists. These sub-branches are usually your root causes. See the above example picture to see what this looks like.
Benefits of Fishbone Diagrams in Root Cause Analysis
The benefits of using fishbone diagrams are:
- Very comprehensive;
- Identifies all major and minor root causes;
- Provides visual reference; and
- Organizes root causes by type of cause.
The cons of fishbone diagrams are:
- No justification for findings; and
- Can be hard to distinguish major and minor root causes.
Related Articles on Using Fishbone Diagrams in Aviation SMS
- How to Use Fishbone Diagrams in Aviation SMS - Walkthrough
- 5 Proven Benefits of a Fishbone Diagram Library in Aviation SMS
- Pros and Cons of Fishbone Diagrams in Aviation SMS
2 – How to Perform 5 Whys Analysis
5-Whys analysis is the most common method used for root cause analysis. Some of the reasons this method is ubiquitous in aviation SMS risk management processes are that the process is:
- Quick;
- Simple; and
- Provides lineage of events.
Unlike some of the other methods, however
- No visual product, like a pretty chart or graph; and
- Somewhat narrow in comparison to other root cause analysis methods.
Performing 5 whys analysis is easy to do. It involves starting at your hazardous condition/risk event, and then asking “Why did this happen?” You will then establish the preceding event/reason that leads to the hazardous condition. Next, you will ask, “And why did this preceding event happen?” Once again, you will establish the next event.
You will repeat this process until you arrive at the root cause. Usually, you will ask "Why?" about 5 times, give or take a couple. You know you have arrived at the root cause when there is no real answer to “why?” In other words, when your answer is “just because,” you have arrived at the root cause.
3 – Using Bowtie Analysis for Root Cause Analysis
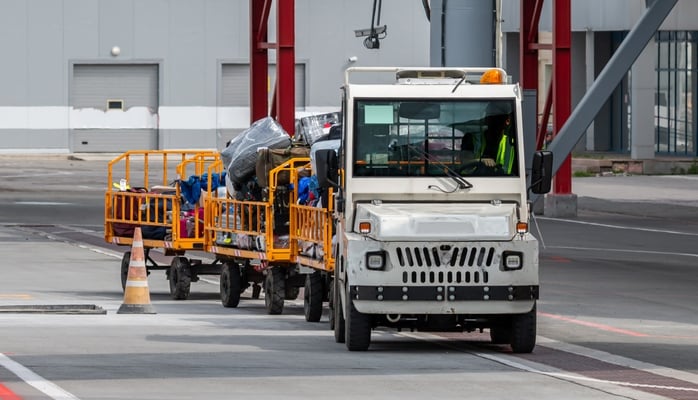
Bowtie analysis is traditionally considered a comprehensive analysis solution, as it establishes everything from root causes to final consequences. Because bowtie analysis is so thorough, it can be time-consuming and abstruse. However, there is no reason organizations can’t use only the “left side” of the bowtie to establish a timeline of all contributing events from root causes to hazardous conditions.
Performing bowtie analysis for root causes is somewhat similar to 5 whys analysis:
- Establish hazardous condition;
- Ask “Why did this happen?” and list the preceding event(s);
- For each preceding event ask “And why did this happen?” – once again, list the preceding events; and
- Like the 5 whys, when your answer is “just because,” you have arrived at a root cause.
Unlike the 5 whys, bowtie analysis:
- Has a visual product to reference;
- Establishes all major (but not minor) root causes; and
- Shows the flow of events from all major root causes to hazardous conditions.
However, reasons you might use 5 whys analysis instead of bowtie are:
- Bowtie analysis is much more time-consuming (better suited for higher risk issues); and
- Bowtie analysis has a learning curve.
Related Articles on Using Bowtie Analysis in Aviation SMS
- What, Why, and How to Use Bowtie Analysis in Aviation SMS
- How to Do Bowtie Analysis in Aviation SMS – 5 Step Walkthrough
- 4 Best Uses of Bowtie Method in SMS Risk Management – Do You Use Them?
Final Thought: Creating Custom Root Cause Analysis Method
It’s also possible to create a custom root cause analysis method that meets your organization’s specific needs. For example, you might create:
- A special type of investigation geared towards root causes; or
- A new type of model (i.e., similar to bowtie, fishbone, TapRoot, etc.).
It’s not so important which method you use. What matters is how well your root cause analysis meets the goals of obtaining the root cause from your analysis.
For a similar method of analysis, see this guide to SMS Shortfall Analysis.
Last updated in May 2025.