Benefits of Integrating QMS and SMS
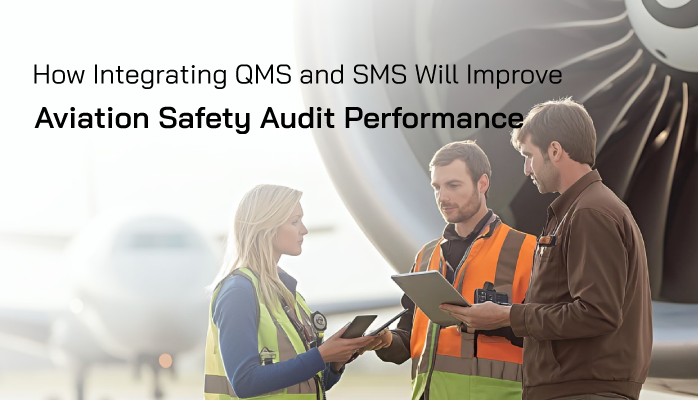
Historically, quality management systems (QMS) and safety management systems (SMS) have been implemented and managed as two entirely separate entities. Today this separation persists in many if not most, companies. This is an unfortunate fact because integrating QMS and SMS provides a great opportunity for organizations to:
- Improve safety performance;
- Increase aviation safety audit results;
- Reduce bureaucratic bloat; and
- Cut overhead costs, while at the same time expanding the safety budget.
Related Articles on Integrated QMS and SMS
- What Are Differences of Aviation Safety Management Systems (SMS) and QMS Programs
- Moving From Quality Management to Integrated SMS and QMS Systems
- 5 Most Important Ways to Integrate Aviation SMS and QMS
Integrated QMS and SMS in Aviation Industry
Despite these benefits, integrating QMS and SMS is uncommon in the aviation industry because:
- It requires overhauling and restructuring the SMS; which
- Requires a time and dedication that safety managers and/or upper management are unwilling to give;
- A quality-safety management system is a relatively new concept without historical precedent; and
- Safety and quality departments are historically distinct business units.
Now, the basic fact is that most aviation SMS implementations have a greater incentive to make changes for compliance reasons rather than safety performance reasons. An SMS with solid bureaucracy and good compliance on paper - whether it's actually performing well or not - doesn’t get hit with regulatory fines.
Despite the fact that the best arguments for integrating a QMS and SMS have to do with safety performance, an SQMS can greatly improve a company’s aviation safety audit performance and audit prep ability.
1 – Fewer Aviation Safety Policies and Procedures to Manage
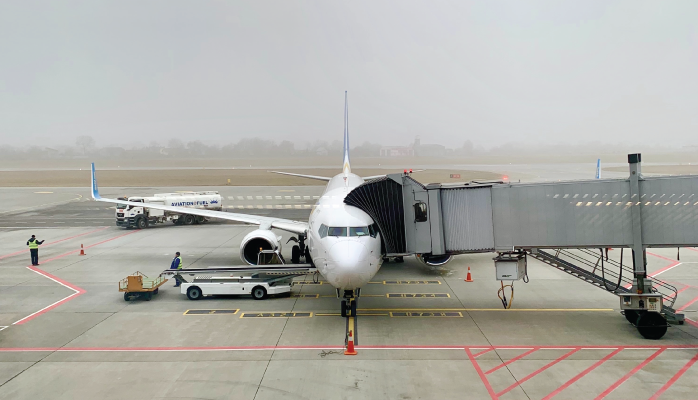
The initial step in integrating aviation QMS and SMS is to inspect the policies and procedures of both the safety program and quality program. The primary goals of doing this are as follows:
- Identify overlapping policies and procedures of QMS and SMS;
- Combine overlapping safety policies/procedures into one QSMS policy/procedure;
- Identify policies and procedures with separation of quality and safety concerns;
- Rewrite such policies to integrate both quality and safety features equally;
- Significantly reduce the total number of policies and procedures in the company; and
- Ensure that bureaucratic functioning of safety and quality is inseparable.
In short, the purpose of the initial step is to cut out the separation of concerns, and in doing so:
- Reduce redundant policies and procedures;
- Allow employees to focus on one procedure for performing a duty rather than a “safety procedure” and “quality procedure” for performing a duty;
- Cut superfluous bureaucratic bloat.
The end result is that safety managers, upper management, and employees have much less to manage. The result is that organizing the QSMS for compliance and preparing for audits is much less involved. It removes the risk that QMS procedures/policies will interfere with SMS procedures.
Related Articles on Integrated Aviation SMS and QMS
- QMS Programs vs Aviation Safety Management Systems (SMS)
- 5 Easy Ways to Combine QMS and SMS in Aviation Operations
- 4 Things to Understand about QMS and SMS in Aviation Risk Management
2 – Better Safety Culture
Ultimately, aviation safety culture is safety performance. One of the primary roadblocks that companies face is the need to perform quality operations and drive revenue. These quality operations often come into direct conflict with safety priorities, and the fact is that the pressure is usually on monitoring quality elements that directly affect financial performance rather than safety initiatives. This can manifest itself in:
- Budget;
- Insufficient or missing safety policies/procedures;
- Risk exposure; and
- Gaps in SMS implementation.
All of the above points can and will reflect poorly on aviation safety culture, and, in consequence, safety audits.
Combining SMS and QMS eliminates the separation of concerns that leads to poor safety performance. In the QSMS model, each policy and procedure combines the concerns of both safety and quality operations.
Moreover, implementing this model requires extensive review and updating of SMS bureaucracy, which will also improve audit performance.
3 – Better Safety Oversight Capabilities
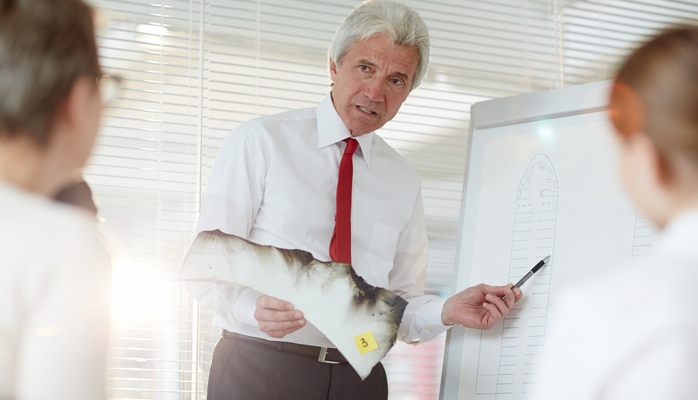
Aviation safety oversight is the ability of safety management to understand the factors involved in the performance of the aviation SMS implementation. Long story short, integrated SMS and QMS operations give safety managers greater control. Mainly, we are talking about control through understanding:
- Safety performance;
- Reasons for success or failure;
- Roadblocks facing aviation SMS implementation; and
- Ability to manage change.
This helps aviation safety audits for three reasons:
- Greater latitude of safety management to make needed changes before the audit because changes don’t have to “workaround” or “contend with” quality operations;
- Better ability to quickly implement changes after audits; and
- Better ability to identify problem areas before audits.
Mainly, better oversight boils down to the fact that in split QMS and SMS programs, the QMS side of operations will always remain a “wild card” in safety performance. Combine the systems, and you incorporate all of the quality operation variables into the scope of safety management.
Related Aviation Safety Audit Articles
- Real Difference Between an Aviation Safety Audit vs. Inspection
- SRM-SA Aviation SMS Audit Preparation - 4 Free Checklist Templates
- Audit Checklist: 10 Things to Prepare for Aviation SMS Audits
Final Thought: How to Integrate
There are 5 main steps to integrate SMS and QMS:
- Ensure upper management support;
- Redesign policies and procedures to incorporate SMS and QMS
- Create goals that are both QMS and SMS;
- Combine quality and safety resources; and
- Implement safety monitoring that is equally quality performance and safety performance.
You may also find the following resource very useful for aviation safety audits:
Last updated October 2024.