What Are Lagging Indicators in Aviation SMS?
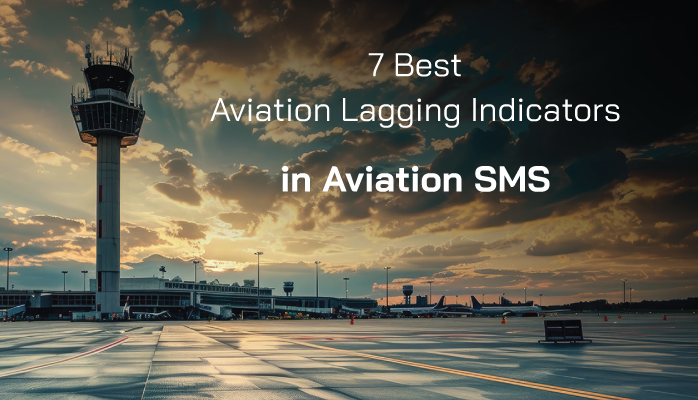
Lagging indicators are an essential element of system performance monitoring in aviation safety management systems (SMS). Safety professionals and accountable executives should become familiar with lagging indicators as these managers are responsible for regularly reviewing organizational safety performance and detecting substandard safety performance.
Lagging indicators show the historical performance of your aviation SMS implementation. They answer 3 essential questions about safety in your risk management program:
- What safety events are happening?
- How many safety events are happening?
- Where are safety events happening?
These questions can be broken down further to ask specific questions about safety performance. Understanding historical safety performance is a prerequisite for identifying underlying causes and leading indicators in your aviation SMS implementation.
Related Articles on Aviation SMS Performance Indicators
- Understand Aviation SMS KPIs Lagging and Leading Indicators
- Stuck on Lagging Indicators in Your Aviation Risk Management Program? Here’s Why.
- What Is a Key Performance Indicator (KPI) in Aviation SMS? - With Free KPI Resources
Importance of Lagging Indicators in Aviation SMS
Lagging indicators will be especially important for newer aviation SMS implementations as those new initiatives attempt to:
- Identify weak areas of the SMS;
- Create key performance indicators (KPIs); and
- Develop relevant control measures.
For more mature SMS implementations, lagging indicators help:
- Validate efficacy of leading indicators;
- Ensure that KPIs remain relevant; and
- Monitor control measures.
Here are 7 essential lagging indicators that safety professionals and accountable executives should be aware of:
1 – Repeat Incidents
Repeat incidents are an extremely effective way to validate the effectiveness of existing risk controls. It’s fairly obvious why.
- When control measures adequately address risk, you should see few to no-repeat incidents; but
- When risk controls are not adequately implemented, or drift into inadequacy, the frequency of repeat incidents will rise in response to degraded risk.
What are repeat incidents? Repeat incidents are noted when essentially the same event happens more than once. By the same event, we mean multiple, separate, seemingly unrelated events that have:
- Same hazard classifications;
- Same root causes; and
- Same risk controls.
These repeat events may not happen in the same location but when they feature the same mechanisms of causes, classifications, and risk controls, they should be considered repeat events. You can easily track this metric in two ways:
- Manually, by keeping a log of repeat events; or
- Automatically, such as with an aviation SMS database, you can link an issue to multiple past issues (i.e., the same past incident).
Related Aviation Risk Management Articles
- Difference Between Hazards, Risks & Control Measures in Aviation SMS
- What Is a Risk Control in Aviation SMS: Meaning, Purpose, Application
- How to Monitor the Effectiveness of Control Measures
2 – Number of Reported Safety Issues Per Month
Monitoring the number of reported safety issues every month has two uses:
- Evaluate safety reporting culture; and
- Identify seasonal trends of safety issues per month.
Number of reported safety issues provides feedback on the quality of aviation safety reporting culture.
As an aviation SMS is implemented, safety management teams would ideally see a steady rise in safety reporting metrics as safety culture improves. Eventually, these numbers should level off and remain consistent. Whenever safety reporting metrics stagnate or safety reporting activity has never been good at a particular company, there are some actions that safety teams should undergo. For example:
- Review safety policy and non-punitive reporting policy. Does the policy resonate with employees? Have the policies been communicated regularly to all employees? Do employees have protection from management for self-reporting safety issues?
- Conduct a safety culture survey. Using a standard safety survey template, are there any identifiable concerns that affect safety reporting metrics? Is there managerial trust? Have employees been properly trained in hazard identification?
- Review safety promotion activities. It is easy for employees to forget about the aviation SMS when they are not reminded. Send out more newsletters, conduct more surveys, and get management involved in promoting the SMS.
Monitoring safety reporting metrics is easily done manually or automatically.
3 – Top 3 Hazard Categories
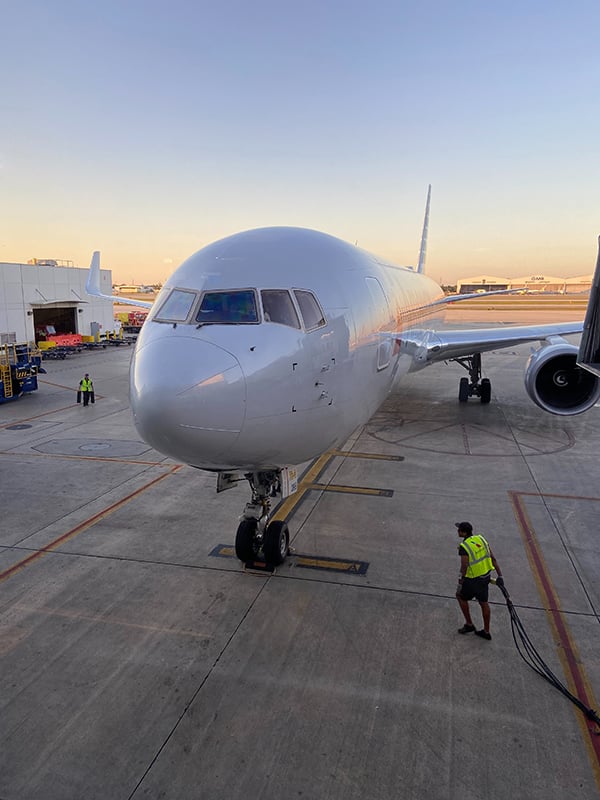
Hazard categories play an important role in understanding the types of safety issues your safety management system is exposed to in the operational environment. Hazard categories are established by your organization as management:
- Reviews operational systems;
- Identify hazards;
- List risks associated with the hazards (credible risk scenarios); and
- Evaluate risk controls for their effectiveness.
In an aviation SMS, identified hazards are placed into a "hazard register," which is simply an organized list of operational and business-related hazards. Since there are literally hundreds of possible hazards affecting an aviation service provider, safety professionals need an efficient tactic to segment hazards in logical ways.
For example, some types of hazard categories you may have in your existing hazard register are:
- Environmental hazards
- Flight ops hazards; and
- Ground ops hazards.
Hazard categories will be associated with treated safety issues, whether they originate from
- safety reporting system; or
- internal audit findings (including assessments and evaluations); or
- external audit findings.
As safety issues are treated in your SMS' documented risk management processes, one of those processes should include "issue classification." Classifying safety issues is important in order to generate meaningful reports and facilitate future predictive risk management activities.
When an issue is classified, its top-level parent category will be associated with the safety issue. Monitoring top hazard categories simply means keeping a running tally of hazard categories as safety issues are classified in the risk management process.
Related Aviation Risk Management Articles
- Difference Between Reactive, Predictive and Proactive Risk Management in Aviation SMS
- What Is the Process of Risk Management in Aviation SMS
- From Reactive to Proactive Risk Management in Aviation SMS
4 – Top 3 Root Causes
Root causes are the foundation of the safety assurance (SA) component of the 4 pillars of SMS. Root causes are the gateway to underlying causes, which are expressed in leading indicator statistics.
Understanding which root causes are most important to your risk management efforts will help you identify underlying causes as well.
Root causes are often broken into three tiers:
- Category;
- Sub category; and
- Root cause.
Like hazard categories, root causes will be associated with safety issues during the risk management process. Root causes are typically determined during the investigation phase of the risk management process. A typical root cause analysis will review the following areas:
- Management responsibility: Organization or person who determines the course of action for a process, who owns the process, and who is accountable for the quality of the process.
- Procedures: Documented or prescribed methods of accomplishing processes.
- Risk controls: Checks or restraints that are designed into a process to ensure that a desired result is achieved.
- Process management: Measures or information assessments to identify, analyze, and document potential problems with a process.
- Interfaces: Interactions between independent processes.
One does not need much imagination to envision how important root causes are for proactive risk management activities. Understanding the frequency of identified root causes in your organization allows management to focus on mitigation strategies that have a far wider range of effectiveness than if the management team focused on individual root causes in isolation.
5 – Number of Procedures/Policies Involved in Issues
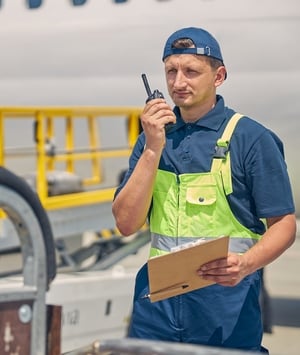
Understanding the failure of your SMS bureaucracy is extremely important for continuous improvement. When your safety policies and procedures aren’t working properly, it’s very difficult for your SMS to maintain an acceptable level of safety (ALoS).
Policies and procedures help guide employees in safe conduct and offer managers assurance that operations will be performed as prescribed. When a policy or procedure is associated with a reported safety issue, it may indicate a breakdown in that guidance. After all, policies and procedures may also be considered as "risk controls" to mitigate risk to ALARP (as low as reasonably practical).
The ability to associate specific policies and procedures with reported safety issues is a way of continuously monitoring the SMS bureaucracy. Associating policies and procedures will happen during the investigation phase of the SMS' documented risk management process. The most logical step in the risk management process to make this association is during the issue classification phase.
Many SMS databases have the ability to classify safety issues according to multiple classification schemes, such as:
- Type of Safety Issue;
- Related Hazards from Hazard Register;
- Location;
- Parts;
- ATA Code;
- Root Cause; and
- Human Factors.
In this case, Policies and Procedures would be simply another one of the ways to classify safety issues. In practice, very few operators classify safety issues according to identified policies and procedures. This becomes a missed opportunity for management to focus on ineffective policies or procedures.
When classifying safety issues according to affected policies and procedures, it makes sense that there should be at least two levels of classification:
- Category (policy or procedure); and
- Specific item.
Related Articles on Aviation SMS Policies
- How to Monitor Aviation SMS' Policies and Procedures?
- Writing & Reviewing Aviation SMS Safety Policies - 4 Free Templates
- How to Review Aviation SMS Safety Policies - Free Checklist
6 – Number of Reported Issues by Role in Company
Safety managers need to know who is reporting safety issues in your company. How else can safety teams know where to focus hazard identification training and safety promotion efforts?
“Roles” is a generic term to classify employees by the function or part they play in aviation SMS. Most of you are familiar with security roles in a software program that determines a user's specific access to information or software functionality. In this case, when we talk about "roles," we refer to how you divide duties and responsibilities. Each type of position in your company with a unique set of duties is considered a “role” in your company. Common roles in the aviation industry include but are not limited to:
- Pilots;
- Cabin crew;
- Operational department heads;
- Aviation maintenance techs; or
- A&P mechanics.
Knowing the number of reported safety issues by role is useful for answering some very important questions:
- Who is involved in the aviation SMS implementation?
- Who is not involved?
- Which user groups are holding back safety reporting culture?
A performant aviation SMS implementation is the result of an organization-wide effort. Complete SMS implementation and ongoing system performance will require a good degree of participation from every level of the organization. This is a great lagging indicator for understanding participation performance across your whole company. This lagging indicator must be made available to the accountable executive!
The accountable executive is responsible for ensuring the aviation SMS is properly implemented and performing in all areas of the organization. By reviewing which user groups are participating in the aviation SMS, a manager can deduce which employee groups are neglecting the SMS.
It is common to see some employee groups actively participate more in the SMS than other parts of the company. Why? I can think of many reasons, but most often, employees are adopting the attitude and behaviors of their supervisors. Operational department heads that embrace the aviation SMS will have employees who are more active in the SMS than employees working under resistant department heads.
Related Aviation Safety Culture Articles
- How Top Management Kills Aviation Safety Culture - With Examples
- 20 Indicators What Good Aviation Safety Culture Looks Like [With Free Checklist]
- 5 Ways to Constantly Improve Safety Culture
7 – Number of Issues by Location
Similar to reported issues by role, it’s also very useful to know where issues are being reported. “Location” is a rather subjective term. When using location as a classification parameter, one has to consider the context of management's expectations. In short, when you think of locations at your company, are you talking about physical locations or logical locations? Everybody needs to be on the same page when using locations as a lagging indicator.
A best practice is to gather location data during the initial safety reporting process, if possible. Alternatively, safety managers may provide these details during the risk management process. For example, in SMS Pro, safety managers can make this association during the issue classification step, and provide 3 tiers of classifying:
- Geographic area (such as city);
- Departments or locations in that geographic area (terminal, hangars, etc.); and
- Distinguishable physical areas in the departments/locations.
Much of how you create the classification tiers will depend on how complex your organization is and how many locations you have. A large organization may even consider having 4 tiers. The point is that you are able to capture classifications that provide a good degree of location detail.
Final Thoughts on Using Lagging Indicators in Aviation SMS
After reading this article, you may think to yourself, "We already use lagging indicators, but we don't have a fancy name for them." It is true. These metrics are not uncommon to find in most aviation SMS implementations.
Arcane risk management terms may seem like jargon to the layperson or to new safety professionals. This is completely understandable. Safety professionals often come directly from the ranks. A college degree is not required to become a safety professional. Nor does a safety professional have to take industry-accepted SMS training courses. Because of the lack of standardization in educating safety professionals, one can easily see confusion among:
- Key performance indicators;
- Leading indicators; and
- Lagging indicators.
How many other indicators can you think of?
Education is a life-long endeavor. We have little recourse. Either learn and adapt or stagnate and become obsolete. We sincerely hope that our educational blog articles offer value to the aviation community. I'm confident that it does, based on the regular feedback from our readers.
In addition to a list of lagging indicators, you should also have a solid list of leading indicators. Here are 40 that should be very beneficial for your SMS implementation:
Last updated in March 2025.